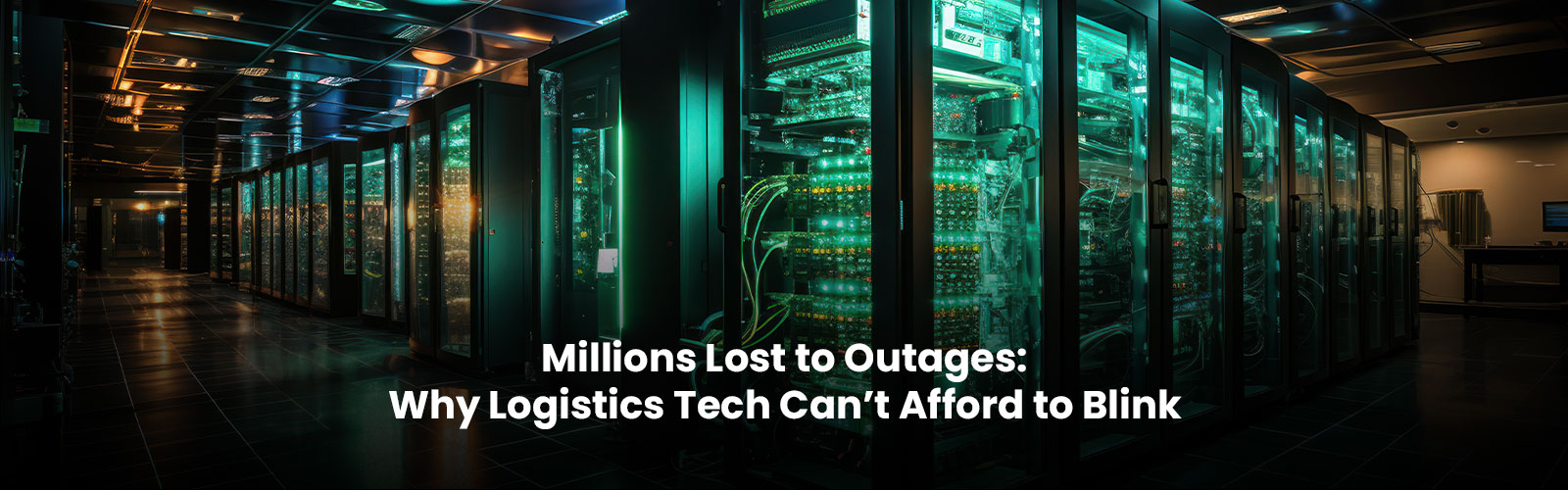
Millions Lost to Outages: Why Logistics Tech Can’t Afford to Blink
In today’s hyper-connected world, logistics management has become the backbone of global commerce. From orchestrating same-day deliveries to maintaining precise inventory control, the modern logistics management system is the nerve center of business continuity. Yet, even the most robust supply chains are susceptible to a silent, costly enemy: downtime.
The High Cost of Downtime
A single outage can cascade through the logistics network, bringing operations to a screeching halt. According to Gartner, the average cost of IT downtime is $5,600 per minute. For logistics operations running at scale, that figure often climbs significantly higher due to compounded losses in transportation, warehousing, and customer service.
Let’s consider a few real-world scenarios that underscore the impact of system failures in logistics:
1. Blue Yonder Outage (2025):
In 2025, major retailers using Blue Yonder experienced a software outage that lasted several hours. This disruption caused widespread delays in inventory restocking, online order fulfillment, and transportation scheduling. Retailers faced not only immediate revenue losses but also damage to customer trust during peak shopping periods.
2. Maersk & NotPetya (2017):
The infamous NotPetya cyberattack hit global shipping giant Maersk, rendering their logistics systems unusable. The result? A $300 million loss and massive global disruption. Operations across ports, terminals, and vessels were stalled, showcasing the vulnerability of digital logistics infrastructure.
3. UPS Sorting Hub Disruption (2022):
A glitch at a major UPS sorting facility in 2022 delayed thousands of packages across the U.S. The issue was traced to a malfunction in the logistics management software controlling conveyor sorting mechanisms. Even a short disruption spiraled into a nationwide delivery delay.
These events underline a clear truth: logistics technology cannot afford to blink.
Why Legacy Systems Fall Short
Legacy logistics management systems were not built to handle the speed, complexity, and volume of modern supply chains. Many were developed with monolithic architectures, making them difficult to update and nearly impossible to scale without risking performance issues.
Furthermore, traditional logistics management software often treats artificial intelligence (AI) as an afterthought. On which is tacked on rather than baked in. As supply chain networks grow in complexity, these systems buckle under pressure, leading to costly outages and prolonged recovery times.
The LogiNext Advantage: Built for Reliability, Designed for Scale
LogiNext, following its strategic restructuring into Stellation Inc, has redefined what it means to deliver resilient logistics management. At a time when businesses are wary of costly disruptions, LogiNext has quietly set a new benchmark.
Here’s how:
1. AI-First Infrastructure:
Unlike other platforms where AI is an enhancement, LogiNext embedded AI into its DNA from day one. This foundational principle allows the system to predict, detect, and self-correct anomalies before they affect performance.
2. Unparalleled Uptime:
Over the past two years, LogiNext has delivered an astonishing 99.99% uptime and a 99.6% crash-free rate – equating to less than five minutes of downtime annually. Most legacy systems can’t promise that in a single quarter.
3. Self-Healing & Graceful Degradation:
Designed with containerized rollouts and self-healing infrastructure, LogiNext ensures operations don’t grind to a halt, even if individual services experience issues. AI-assisted graceful degradation means partial functionality is maintained until full service is restored.
4. Scalable Growth with Stability:
Since becoming Stellation Inc, LogiNext has achieved 1.2x growth, scaling its user base and geographic footprint without compromising on reliability. This is a rare feat in the logistics technology space.
This makes LogiNext not just a logistics management software vendor, but a strategic partner in ensuring business continuity.
The Strategic Value of Uptime in Logistics Management
When a logistics management system is always online, the benefits ripple across the entire supply chain:
1. On-Time Deliveries:
With uninterrupted access to routing, inventory, and delivery data, logistics teams can ensure products reach customers on schedule. Even during peak demand periods.
2. Real-Time Visibility:
Continuous uptime enables live tracking of shipments and assets, empowering proactive decision-making and customer updates.
3. Warehouse Efficiency:
Downtime in warehouse systems can lead to missed picks, misloads, and idling staff. A reliable logistics management system keeps workflows moving seamlessly.
4. Customer Trust & Brand Loyalty:
Consistency breeds confidence. Customers who experience timely, predictable deliveries are far more likely to return – something that’s impossible to guarantee with unreliable tech.
Logistics Management in the AI Era
AI is no longer a future concept, it’s a present-day necessity in logistics management. Predictive maintenance, dynamic routing, demand forecasting, and risk mitigation are all powered by intelligent algorithms that rely on uninterrupted data flow.
LogiNext’s AI-powered logistics management software turns data into a strategic asset, not a liability. It detects emerging patterns, optimizes delivery routes in real time, and offers insights that reduce waste and enhance service levels.
And because the AI is native and not layered in later, it functions more reliably under stress, delivering both performance and peace of mind.
Final Thoughts
In an industry where minutes of downtime can equate to millions in losses, choosing the right logistics management system is not a luxury. It’s a necessity. Events like the Blue Yonder outage, Maersk’s NotPetya nightmare, and the UPS sorting hub failure are cautionary tales that reinforce one simple message: logistics tech can’t afford to blink.
LogiNext’s forward-thinking architecture, AI-driven stability, and industry-leading uptime make it a cornerstone of modern logistics management. For enterprises seeking a dependable, scalable, and intelligent logistics management software solution, the choice is clear. Book a demo to know more.
46
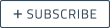
@LogiNext